
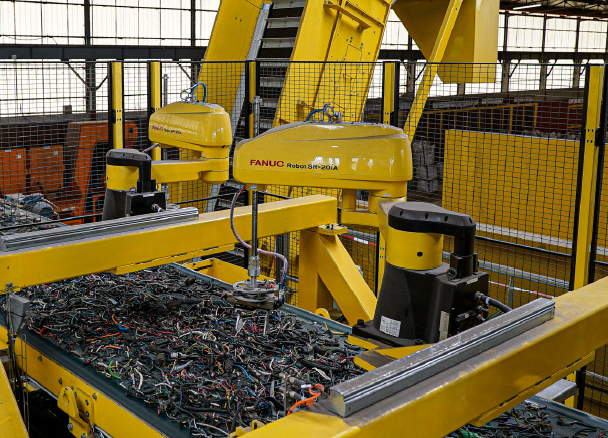
Le « process jaune » pour davantage de pureté
Publi-rédactionnel
Posté par : Juliette Ulmann 14.11.2023 à 15h00
Le groupe Vessière est spécialisé dans la récupération et le recyclage de métaux et de matériaux électriques et électroniques. Il possède trois entités.
La première, établie à Dreux depuis 130 ans, traite de l’aluminium, du cuivre, de la ferraille et d’autres métaux afin de les réintroduire dans les circuits de production industrielle. La deuxième, Lusofer, a été créée à Vitry-sur-Seine il y a une décennie, par Rui Marques, associé du groupe. Lusofer collecte 90.000 tonnes de métaux par an et traite également des déchets d’équipements électriques et électroniques (DEEE) en partenariat avec l’éco-organisme Ecosystem. C’est sur le troisième site, celui de Longueil-Sainte-Marie, que le groupe Vessière a mis au point un procédé unique de recyclage des câbles électriques.
Produire un cuivre encore plus pur
Au terme de trois années de recherche et développement, le « process jaune » a été assemblé en amont de la chaîne de broyage des câbles sur le site situé dans l’Oise. Ce nouvel équipement, formé de 31 machines, vise à dépolluer des déchets de 2 à 5 cm de diamètre et à les séparer de pièces indésirables : prises, gaines métalliques ou en plomb, connexions inox ou aluminium… Le process jaune s’ajoute aux process rouge, bleu et orange, lesquels permettaient déjà de séparer différents composants métalliques et plastiques des câbles (aluminium, PVC, caoutchouc, etc.). En sortie d’usine, l’association de ces procédés de purification permet d’obtenir des lots de grenaille de cuivre à 99,99 % de pureté.
« Nous avons cherché comment améliorer encore davantage la qualité des produits que nous vendons ensuite à nos clients, pour avoir moins de 12g de plomb, 10g d’aluminium, ou encore 25g de zinc, en s’approchant de zéro gramme de ces métaux à la tonne de cuivre recyclé sortant d’usine », indique Fabien Vandamme, actionnaire du groupe. « Il a donc fallu réussir à supprimer les indésirables contenus dans les lots de vieux câbles qui nous arrivent. Notre nouveau process, composé de 31 machines, est capable de cisailler les rouleaux de câbles en segments de moins de 30 cm en moyenne, de les déferrailler, de les passer au crible et de dépoussiérer les volumes entrants avant la séparation magnétique des déchets en acier ou d’autres matériaux. Le tout se fait de façon automatisée, sous le contrôle d’un seul opérateur ».
Le procédé a été conçu sous forme de modèle numérique « avec un logiciel Solidworks en 3D », détaille Sergueï Gladkov, ingénieur des mines en chef. « Nous avons communiqué avec les sous-traitants usineurs et modifié plusieurs fois les dimensions requises pour finaliser au mieux la chaîne de traitement ».
Viser l’excellence
L’unité de recyclage du groupe était déjà parvenue à un niveau de pureté de la grenaille de cuivre supérieur à 99,9 %. Les dernières innovations visent à obtenir, en bout de chaîne industrielle, des big bags de grenaille de cuivre d’une pureté inégalée, s’approchant des 100 % du cuivre primaire issu de cathodes.
« Le bureau d’études du groupe et son ingénieur des mines en chef, Sergueï Gladkov, également docteur en magnétisme, ont réussi à descendre bien en-dessous des normes de tolérance en vigueur de moins de 80 % exigées par ses clients fondeurs pour tous les résidus de métaux non ferreux indésirables tels que le plomb, l’aluminium, le laiton et les inoxydables », précise Fabien Vandamme.
En plus d’améliorer la qualité du cuivre produit, ce nouveau process va aussi soulager le laboratoire d’Aurélie Roux, chimiste en charge de l’analyse et de la validation quotidienne du taux de pureté des échantillons de métal rouge. Une fois refondu, celui-ci est testé en permanence avec un spectromètre à cristaux et un arc électrique à 1.300 °C.
En pratique : déroulé des opérations
Sébastien Lachieb, directeur du site, revient sur les toutes premières étapes réalisées sur place : « Lorsqu’un camion arrive sur site, il se gare sur le pont bascule équipé d’un portique de détection de la radioactivité. Le poids du chargement est enregistré puis nous vérifions la qualité et la conformité du chargement par rapport aux informations transmises par le fournisseur. Une fois déchargé, le chargement est contrôlé visuellement par 3 opérateurs. Ensuite, nous procédons au traitement de la matière ». Guillaume Mesureur, responsable de la production, poursuit : « Après la phase de tri des déchets, la matière passe par une première cisaille rotative, puis dans une succession de broyeurs ».
Un investissement de 3,7M€
Conçu en interne par les experts du groupe, le développement et l’assemblage du procédé jaune a fait l’objet d’un investissement de 3,7 millions d’euros. Après de nombreux échanges avec les fournisseurs des machines, le montage de la chaîne de traitement a été effectué en interne. Il a débuté en décembre 2022 et s’est poursuivi jusqu’à l’été 2023.
« Nous voulons rester maîtres de notre destin, choisir les éléments à assembler, viser l’amélioration continue des procédés de notre entreprise. Nous faisons ici un pas en avant dans notre dispositif de recyclage, en installant ce nouvel outil de valorisation des déchets de câbles situé en amont de nos autres procédés, qui nous avaient déjà permis d’arriver à 99,9 % de pureté du cuivre grâce à des brevets déposés par le groupe », poursuit Fabien Vandamme.
Fin juillet, la phase de test de la nouvelle unité de prétraitement des câbles à recycler a débuté. Les robots Fanuc, montés en ligne après la première phase de broyage des déchets, ont alors pu réaliser un auto-apprentissage : leur capacité mémorielle leur permet de reconnaître près de 40.000 objets ou formes à sortir du système de triage. Ils peuvent saisir jusqu’à 7.200 pièces par heure.
Après le tapis de circulation des segments de câbles broyés se trouve un équipement du constructeur allemand Steinert. Dotée de rayons X, la machine repère les débris en aluminium et les souffle aussitôt en dehors du circuit afin qu’ils soient récupérés un peu plus loin.
Amélioration continue
Dans un esprit « d’amélioration continue et de protection des équipements », le process jaune a aussi la particularité de « sortir du circuit d’éventuels déchets dangereux tels que les piles au lithium-ion, des pièces de mécanique ou de fixation, comme des boulons ou des vis en acier », explique Fabien Vandamme.
Les technologies de pointe du site de Longueil-Sainte-Marie optimisent le rendement de l’usine : la capacité de traitement passe à 13 tonnes par heure de câbles à recycler, et ce 24h/24.
Une évolution saisissante
Les temps ont bien changé, depuis l’implantation du groupe Vessière à Dreux en 1892 : « La progression de notre métier sur quatre générations de la famille Vandamme est saisissante, reprend Fabien Vandamme, depuis la collecte à la main des peaux de lapin, de vieux chiffons et métaux, avec aujourd’hui l’utilisation des robots pour détecter et sortir les éléments indésirables du jeu grâce à leur capacité de reconnaissance des intrus ».


La détection de filigrane UV, outil de traçabilité du futur ?
Paris.– Pellenc ST, collabore avec Polytag, sur l’intégration d’une technologie innovante de détection de filigrane UV invisible destinée à améliorer la précision du tri des emballages. Cette solution, intégrée sous forme de module...
